Disco-ers,
I'm attempting to rebuild my watts link in my 2000 US Spec Disco 2 w/rear air.
The three center bushings came in and out as expected (with metal sleeves on the bushings) -- But for the love of god use a "shop press" - it makes it so much easier.
The rub is the "outer bushings" or "Track Bar bushing" -- Part number RGB100970G (not there is a RGB100970 - which I believe is a LR OG part)
https://www.roverparts.com/suspensio...gs/RGX100970G/
These bushings have a plastic sleeve instead of metal, and it seems like maybe a teflon coating.
For the life of me I can't get it in to the arm of the watts link.
I put a caliper on the OLD bushing that came out, the New bushing, and the hole in the Track Bar Arm, and it does not make sense:
Old Bushing: 43mm
New bushing: 44mm
Track Bar opening: 42mm
I called Atlantic British and they confirmed that the correct bushing is 44mm. So I have the right part!
PS - I'm using this video as a guide, but not having any luck:
what is the trick here? I've tried 'chamfering" the track bar opening (as a video suggested)
Help!
Thanks!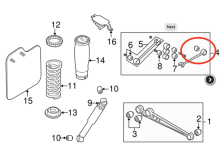
I'm attempting to rebuild my watts link in my 2000 US Spec Disco 2 w/rear air.
The three center bushings came in and out as expected (with metal sleeves on the bushings) -- But for the love of god use a "shop press" - it makes it so much easier.
The rub is the "outer bushings" or "Track Bar bushing" -- Part number RGB100970G (not there is a RGB100970 - which I believe is a LR OG part)
https://www.roverparts.com/suspensio...gs/RGX100970G/
These bushings have a plastic sleeve instead of metal, and it seems like maybe a teflon coating.
For the life of me I can't get it in to the arm of the watts link.
I put a caliper on the OLD bushing that came out, the New bushing, and the hole in the Track Bar Arm, and it does not make sense:
Old Bushing: 43mm
New bushing: 44mm
Track Bar opening: 42mm
I called Atlantic British and they confirmed that the correct bushing is 44mm. So I have the right part!
PS - I'm using this video as a guide, but not having any luck:
what is the trick here? I've tried 'chamfering" the track bar opening (as a video suggested)
Help!
Thanks!
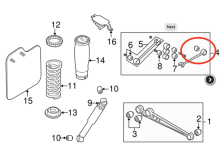
Last edited: